Project of the Year: Special Projects Category
Ohio State "Horseshoe" Renovation
Owner
Ohio State University
Columbus, Ohio
Project Engineer/Designer
IC Construction
Akron, Ohio
Repair Contractor
Osborn Architects & Engineers
Cleveland, Ohio
Material Suppliers
Sika Corporation
Lyndhurst, New Jersey
Triventure
Columbus, Ohio
The Ohio State Buckeyes, perennial contenders for the Big Ten and National Championship in college football can attribute part of their success to their loyal fans and the fabled stadium where the home games are played. The “Horseshoe” is sold out for every home game, and nearly 32 million fans have passed through the turnstiles over the stadium’s 75-year history. However, all this activity caused the stadium to be in dire need of repair. The school trustees decided to embark on a construction program, the first major renovation project ever done on Ohio Stadium.
To maintain the stadium’s distinctive horseshoe shape and architectural details, while modernizing the facility and adding to the capacity, the designers decided to excavate the field and create a new playing surface 14 and 1/2 feet lower the than existing one. This not only improved visibility but allowed for additional seats, restrooms, hospitality suites, concession facilities, and six new elevators to be installed. New ramps and wider aisles allowed the stadium to comply with the American Disability Act.
The net gain in the seating capacity is 7000 bringing the total capacity of the stadium to approximately 98,000. The revenue generated from the sale of new Hospitality Suites and Club Seats accounted for 80% of the $187 million needed to support the project, of which the extensive concrete repair and strengthening accounted for $13 million. All three decks of the stadium were in bad shape and needed to be removed and replaced. The worst area was the north side of the C deck, where ready-mixed concrete was used as a full-depth repair. In other areas, a polymer-modified repair mortar was hand-applied using shotcrete equipment.
During the course of renovation, it was discovered that the existing concrete columns were not properly reinforced. Despite having served its function for over 75 years, the columns needed to be strengthened in order to comply with current building code. An innovative carbon fiber reinforced polymer (CFRP) system was designed and installed in a rapid fashion, allowing the fast-track project to remain on schedule.
The renovation of the stadium was a three-year project, beginning in December 1998, with work being completed in stages so as not to interfere with the home games of the Ohio State Buckeyes. During the course of construction, much of which took place during the cold winter months, not one home game was cancelled or postponed. To get the stadium ready for both the 2000 and 2001 home openers, the work schedule was accelerated, but milestones were met.
Award of Excellence
Buchanan House Repair High-Rise — C.A. Lindman, Inc.
Award of Excellence: High-Rise Category
Buchanan House Repair
Arlington, Virginia
Submitted by C.A. Lindman, Inc.

Owner
Charles E. Smith Companies
Arlington, Virginia
Project Engineer/Designer
Theobold Bufano & Associates
Washington, D.C.
Repair Contractor
C.A. Lindman, Inc.
Jessup, Maryland
Material Suppliers
American Stone Mix
Towson, Maryland
Mameco
Beachwood, Ohio
Sika Corporation
Lyndhurst, New Jersey
The Buchanan House is a 15-story upscale apartment property located just outside of Washington DC in the Crystal City section of Arlington, Virginia. Its proximity to Reagan National Airport, to the Pentagon, to the DC-area high tech corridor and to the nation’s capital make the Buchanan House a popular address fro the military personnel, airlines employees, government workers and other professionals. The building is a 25-year old concrete structure with cast-in-place concrete balconies.
Since its construction, Buchanan House had received very little exterior maintenance. Significant balcony deterioration problems were evident when it was purchased in 1908 by nationally-prominent developer and property manager The Charles E. Smith Companies. Shortly after the purchase, the new owner saw pieces of the pre-cast concrete balcony rails and balcony slabs break loose and fall to a heavily-trafficked sidewalk below. No injuries occurred due to the incidents, but repair measures were obviously necessary. In order to address these safety issues, and to bring the building up to their operating standards, the CE Smith Companies initiated a repair program to restore the structural integrity of the 367 balconies, and improve the appearance of the property.
The original pre-cast concrete rail systems were secured to the balconies by steel rail posts embedded in the slabs. Weathering of any sealant originally installed at the embeds had led to rusting and deterioration of the rail posts. Rust expansion of the posts in turn caused spalling of the rail post pockets, and eventually of the balcony slab edges. This spalling exposed reinforcing steel in the slabs, which also rusted, causing both more spalling and extensive cracking on the tops of the slabs. Visual inspection and sounding of balcony slabs indicated that the falling concrete incidents were not isolated occurrences, but were evident of systemic problems.
The renovation of the stadium was a three-year project, beginning in December 1998, with work being completed in stages so as not to interfere with the home games of the Ohio State Buckeyes. During the course of construction, much of which took place during the cold winter months, not one home game was cancelled or postponed. To get the stadium ready for both the 2000 and 2001 home openers, the work schedule was accelerated, but milestones were met.
Freedom Tower Renovation Historic — Structural Preservation Systems, Inc.
Award of Excellence: Historic Category
Freedom Tower Restoration
Miami, Florida
Submitted by Structural Preservation Systems, Inc.
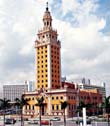
Owner
Freedom Tower Renovation Project
Miami, Florida
Project Engineer/Designer
Donnell, Duquesne & Albaisa, PA
Miami, Florida
Repair Contractor
Structural Preservation Systems, Inc.
Pompano Beach, Florida
Material Suppliers
CSR Rinker Materials
West Palm Beach, Florida
Sto Corporation
Atlanta, Georgia
The Freedom Tower in Miami, Florida, a 75 year-old architectural landmark and enduring symbol of resilience in the face of adversity, was built in 1925. The seventeen-story stucco office tower is a prime example of Spanish Renaissance revival style. Between 1962 and 1974, it became Miami’s “Ellis Island,” where 400,000 Cuban refugees fleeing the communist regime of Fidel Castro were processed.
In 1997, a Cuban-American businessman acquired the building, with plans for a complete renovation to commemorate the Cuban refugee experience. By then, the building’s aesthetics and structural elements were severely degraded, and the building was, in fact, on its way to collapse.
Restoration work started in the parking garage where testing revealed that the original concrete mix was about half of what structural concrete’s compressive strength should be. Practically every beam and column in the garage, and the entire garage slab needed repair.
Overhead, partial-depth slab repairs utilized form-and-pump placement. The soffit repair included adding approximately 1″ of extra concrete to the original construction. To preserve the structural integrity of the slab, work was conducted in a phased “checkerboard” manner.
Columns were also repaired using a form-and-pump technique that turned out to be extraordinary. Because 100% of the column cross-section was removed, the work required extensive shoring of the upper floors and pinning of the whole shoring assembly to the columns above.
Beam repairs were also required throughout the structure, including concrete-encased I-beams on certain floors. Many beams required full-depth replacement, and some slabs were strengthened by a composite strengthening system to withstand additional load-bearing requirements.
Miami’s freedom Tower is a striking symbol not only for architectural preservationists, but also for the multitude who trace their first taste of freedom to its halls. It is also confirmation of today’s technology for the repair industry to successfully complete challenging restorations of this type.
The Joint Water Pollution Control Plant Repair Municipal — Sika Corporation
Award of Excellence: Municipal Category
Joint Water Pollution Control Plant Repair
Carson, California
Submitted by Sika Corporation
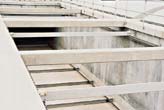
Owner
Los Angeles County Sanitation District
Carson, California
Project Engineer/Designer
Construction Technology Laboratories
Skokie, Illinois
Repair Contractor
J.F. Shea Construction, Inc.
Walnut, California
Material Suppliers
Sika Corporation
Lyndhurst, New Jersey
The Joint Water Pollution Control Plant (JWPCP), owned and operated by The County Sanitation Districts of Los Angeles County (Districts) is one of the largest wastewater treatment plants in the world. The pure oxygen secondary treatment process produces high quality secondary effluent; however, the process also results in an environment that is highly corrosive to both the equipment and the concrete surfaces. After approximately 16 years of service some of the concrete structures had experienced up to a 1/2 in. loss of section due to the exposure to the aggressive environment. Continued loss of section would no doubt eventually lead to attack of the reinforcing steel and ultimately structure failure.
The District began a research effort to evaluate material that would protect the concrete from further damage and provide enhanced protection for the steel reinforcement. The search ultimately lead to the evaluation of several very-dense, low-permeable, cementitious-based materials. These materials would be mechanically ‘shot’ onto the prepared substrate in the appropriate manner (wet or dry) and evaluated for various important physical properties including absorption, permeability and bond. A comprehensive test program was completed to evaluate the performance of the materials when applied, and to identify any project-specific concerns pertaining to surface preparation, application, testing, finishing and curing. Once the selection of the appropriate material was completed, the project specification was finalized.
The work, completed in the secondary effluent conveyance structures, could only be done when the entire secondary treatment facility was shut down. The Districts obtained special approval from the regulatory agencies to complete all repairs and return to full operation within 90 days. The Districts would be subject to substantial fines and penalties if this deadline was not met. Therefore, the selection of material and method of application were especially important to ensure a problem-free completion of the work with the highest quality and without any delays.
2nd and Plankinton Municipal Parking Structure Renovation Parking Structures — Consulting Engineers Group grey line
Award of Excellence: Parking Structures Category
2nd and Plankinton Municipal Parking Structure Renovation
Milwaukee, Wisconsin
Submitted by Consulting Engineers Group
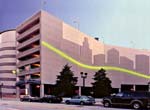
Owner
City of Milwaukee, Department of Public Works
Milwaukee, Wisconsin
Project Engineer/Designer
Consulting Engineers Group
Mount Prospect, Illinois
Architect
Lisa Kennedy, AIA
Milwaukee, Wisconsin
Repair Contractor
National Restoration Systems, Inc.
Rolling Meadows, Illinois
The 35 year-old Second and Plankinton parking garage is an important asset in the Milwaukee’s growing entertainment district. The city’s decision to restore it has resulted in a renewed parking resource that exceeded expectations.
Structural modification to enhance safety and efficiency involved the repair of all deteriorated joists, walls, stairwells, delamination of the slabs and repairs to the concrete slabs and walls of the double-threaded helix. Construction joints and slabs were repaired and sealed, and minor repairs were made to the structure’s beams and columns. Hydrodemolition removed delaminated concrete and prepared the surface for an overlay on the cantilevered helix slabs, the pan joist slab system and on other selected concrete areas.
Preventative measures were developed to reduce deterioration, including varying the corrosion inhibiting and waterproofing strategies used throughout the garage. On the cantilevered helix slabs and the pan joist system, epoxy coated reinforcing bars and a microsilica concrete overlay were applied. The pan joist slab system on level 2 and 3 also received a traffic-bearing membrane coating. On the garage’s top two levels, the concrete was patched and a traffic-bearing membrane coating was applied. A detailed annual maintenance program was implemented.
Architectural modifications to the garage were dramatic and complemented surrounding structures. The north façade features a cityscape with a neon band to create visual interest. The helix enclosure and railings were painted to soften the interior and compliment adjacent buildings. A brighter and more prominent lobby and offices will better serve patrons and staff. New signs and graphics were installed to enhance wayfinding. Improvement to the interior environment involved painting and lighting.
The results of the restoration have more than exceeded the city’s goals. There is a waiting list to get into the structure, and the quality parking has attracted new businesses, which use the garage for parking.
Rooftop Pool Renovation at the Willoughby of Chevy Chase Special Projects — Choice Restoration Services, Inc.
Award of Excellence: Special Projects Category
Rooftop Pool Renovation at the Willoughby of Chevy Chase
Chevy Chase, Maryland
Submitted by Choice Restoration Services, Inc.
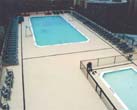
Owner
The Willoughby of Chevy Chase
Chevy Chase, Maryland
Project Engineer/Designer
Wiss, Janney, Elstner Associates, Inc.
Fairfax, Virginia
Repair Contractor
Choice Restoration Services, Inc.
Baltimore, Maryland
Material Supplier
Tremco, Inc.
Beachwood, Ohio
Rooftop pool and adjacent area renovations were undertaken on this building as a result of years of deterioration and material failures. Full investigative services were provided to evaluate options and design criteria. As with all restoration projects, a balance between cost and retrofit system performance drove the design. Additionally, the restoration demanded performance with the least inconvenience to the day-to-day operations of the facility. To this point, specific to this project, was the need to complete the task at hand in the midst of a typical Mid-Atlantic winter.
Unique limited site access, dictated by the approximate 250-foot elevation of work and tight urban-type site footprint, made this a particularly unique and challenging project. Equipment mobilization, material placement and weather concerns played a major role in the planning and implementation of the project. The project team pooled its collective and extensive experience to adapt and overcome the pitfalls of this challenging undertaking.
Ashford Perimeter Parking Garage Strengthening Strengthening — Structural Preservation Systems, Inc.
Award of Excellence: Strengthening Category
Ashford Perimeter Parking Garage Strengthening
Atlanta, Georgia
Submitted by Structural Preservation Systems, Inc.
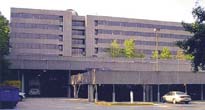
Owner
Glenborough Realty Trust
Atlanta, Georgial
Project Engineer/Designer
Simpson Gumpertz & Heger
Arlington, Massachusetts
Repair Contractor
Structural Preservation Systems, Inc.
Tucker, Georgia
Material Supplier
Master Builders, Inc.
Cleveland, Ohio
The Ashford Perimeter Parking Garage supplies approximately 1000 parking spaces for a commercial office. The lowest level of the four-level garage is on-grade with three above in a terraced configuration. No internal structural ramps exist as each level is accessed on grade. The deck is 8 in. thick, 2-way, post-tensioned, flat slab.
The column-strip post-tensioning in the E-W direction was inadequate. A repair was developed using a heavily-reinforced Gunite beam added to the underside of the slab column strip. Soon after, delaminations between some beams and slab were noticed. An NDT investigation (pulse velocity test), concluded that approximately 30 percent may have more than 40% delamination. The engineering firm then recommended more NDT inspection utilizing impact echo. Of the 133 beams tested, 105 showed some delamination, and 19 had 33% or more delamination.
The first phase of the repair included an in-depth in-situ load testing of the existing slab under various conditions that existed as well as strengthened with FRP sheets. A load testing procedure was proposed to provide a non-destructive demonstration of the performance of structural components, utilizing hydraulic jacks to induce force equivalent to those resulting from distributed loads
Test results indicated that the beam in the E-W direction with a minimum of 70% bond performed well. A span with no beam demonstrated poor performance. Results also showed CFRP strengthened slabs (after removing the Gunite beams) were satisfactory. Accordingly, 19 locations E-W beams would remove and the slab would be strengthened with CFRP sheet. Typical span in the N-S direction were found to be acceptable without additional upgrade.
Large overstress in the E-W end spans and excessive deflection to the 2nd level cantilever required another strengthening approach. External steel-framing was installed reducing the clear span, and additional steel supports were installed under the cantilever slabs. At steel support points, “pancake” jacks were permanently installed to engage the steel frame.
Repair of Crib Point Jetty Transportation — MBT Australia Pty Limited
Award of Excellence: Transportation Category
Repair of Crib Point Jetty
Victoria, Australia
Submitted by MBT Australia Pty Limited
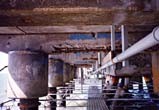
Owner
Toll Geelong Port
Geelong, Victoria, Australia
Project Engineer/Designer
Maunsell McIntyre Pty Limited
Melbourne, Victoria, Australia
Repair Contractor
Finn International
Rozelle, New South Wales, Australia
Material Supplier
MBT Australia Pty Limited
Oakleigh, Victoria, Australia
Highlighting the benefits of advanced concrete repair and protection material technology, the recently completed repairs to the Crib Point Jetty incorporated the use of a truly innovative shotcrete repair mortar, which features a state-of-the-art corrosion inhibitor.
Located in Westernport Bay Victoria, Australia, the Crib Point Jetty is a concrete pier and beam structure which incorporates an “Approach way Arm” section, together with two “Jetty Head” sections. A detailed maintenance inspection of the structure uncovered substantial spalling. Cracking and degradation of many of the concrete piers and beams along the “Jetty Head #1” and “Approach way Arm” sections of the structure. As expected, the survey demonstrated that this damage had been caused by significant corrosion to the structure’s steel reinforcement resulting from constant exposure to the harsh marine environment.
Following the removal of all degraded concrete and steel reinforcement, together with the integration of new reinforcement where required, repairs to the concrete were made using a shotcrete repair mortar with an integrated migrating corrosion inhibitor that reduces further occurrences of corrosion within the structure’s steel reinforcement. This repair mortar provides an innovative and effective repair and protection solution to one of the concrete construction industry’s most costly problems—damage caused by the corrosion of steel reinforcement.
Repair of Port Edwards Dam Water Systems — STS Consultants Ltd.
Award of Excellence: Water Systems Category
Repair of Port Edwards Dam
Port Edwards, Wisconsin
Submitted by STS Consultants, Ltd.
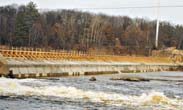
Owner
Domtar
Port Edwards, Wisconsin
Project Engineer/Designer
STS Consultants, Ltd.
Green Bay, Wisconsin
Repair Contractor
Lunda Construction Company
Schofield, Wisconsin
Material Supplier
Wisconsin Valley Concrete Products
Wisconsin Rapids, Wisconsin
Potter Form and Tie
Appleton, Wisconsin
A major paper company owns a rock-filled, timber crib dam across the Wisconsin River in Central Wisconsin. The structure was built in the late 1840s in order to pool water to float timber to the pulp mill and power the grindstones of the pulp mill.
Over time, the spillway structure of the dam had been raised, a concrete cap constructed, tainter gates added, and the pulp mill grindstones replaced by hydroelectric generators.
The original scope of the project was to address repairs required to the existing concrete cap of the spillway, construct a downstream wall founded on bedrock, and straighten the horizontal and vertical alignment of the cap of the structure. The reconstruction design was completed by another firm. The owner delayed the work until 1999, performing “as needed” maintenance in the interim.
The engineering consultant was originally contracted for a basic field service inspection of the concrete and reinforcing steel. Additionally, the consultant was asked to assemble a Federal Energy Regulatory Commission (FERC) Construction Quality Inspection Program. As the project progressed, the consultant’s role expanded significantly. An investigation of the subsurface conditions of the structure and the completion of a new design (to accommodate working under unforeseen conditions) were also needed. This new design was completed in an extremely short period of time with cooperative teamwork between the owner, primary contractor, and FERC. The design took into account construction material cost, constructability, and time remaining in the Wisconsin construction seasons.